The Impact of 3D Print Heat Modeling on Print Quality
If you’re a 3D printing enthusiast, then you’ve probably faced the odd print failure at some point. Warping, cracking, or uneven layers can leave you frustrated after putting in a lot of effort. You’re not alone, though! Heat distribution is one of the main causes of such issues. 3D print heat modeling can help with it. You may avoid many of these issues and get better results by knowing how heat moves through your print. Let’s examine heat modeling’s definition, significance, and potential to produce faultless 3D prints.
What is 3D Print Heat Modeling?
3D print heat modeling is basically about controlling the 3D print’s temperature during production. A specific temperature must be reached before your 3D printer can extrude material. The catch is that warping and other unsightly flaws may result if the heat isn’t distributed evenly throughout the print. To avoid these issues and guarantee that your print turns out perfectly, heat modeling is a technology that predicts and regulates how the heat is dispersed throughout the process.
Why is Heat Distribution So Important in 3D Printing?
3D printing can be similar to cake baking. A cake that is charred on one side and raw on the other could result from uneven oven heating. 3D printing works on the same basis. Issues including uneven surface quality, poor layer adhesion, and warping can result from uneven heat distribution. Some areas of the print may shrink, bend, or crack if it cools down too soon. The proper amount of heat must be applied uniformly for a smooth, superior finish.
How Does Uneven Heat Affect Print Quality?
This is where frustration may set in. Certain areas of the print cool more quickly than others when heat isn’t dispersed uniformly. Warping, in which the print’s edges begin to pull off the bed, is never a good sign. Additionally, you might notice fractures forming, particularly if the material cooled too quickly and the layers weren’t adhering correctly. It’s like attempting to glue two pieces of plastic together, only to have one side be too cold for the glue to stick. In summary, uneven heat can cause problems for your print’s entire structure.
The Role of 3D Print Heat Modeling in Preventing Warping
Heat modeling is the answer if warping is your worst nightmare. It helps avoid the dangerous temperature gradients that lead to warping. How? By making sure that heat is applied evenly. You may lower the chance of your print warping or cracking by adjusting the settings. These are nozzle temperature and bed heat or modeling the movement of heat throughout your print before you even begin printing. Consider establishing a template for the proper behavior of the heat. Heat modeling helps you with that!
How Does 3D Print Heat Modeling Work?
In general, it’s an automated form of predicting the trend of heat during printing. The software considers a variety of factors, including the material being used, the printer’s heat source, and even the geometry of the object being printed. After simulating the distribution of heat throughout the print, it offers you advice on how to modify the parameters to maintain a uniform heat flow. It is comparable to having a personal assistant who is highly skilled at assessing the situation and warning you when it is going to spiral out of control.
Relevant Studies on Heat Distribution and 3D Print Quality
Two key studies highlight the importance of heat management in 3D printing. The first, “Influence of Printing Parameters on the Thermal Properties of 3D-Printed Concrete Structures” on ScienceDirect, investigates how various printing parameters affect the thermal conductivity and defect development in 3D-printed concrete. This research underscores the significance of controlling heat distribution to maintain print quality and structural integrity. The second study, “Improving the Impact Strength and Heat Resistance of 3D Printed Models” on ResearchGate, focuses on how extrusion temperature and print speed influence the mechanical properties and heat resistance of PLA, emphasizing the role of thermal processing in enhancing print quality. Together, these studies provide valuable insights into the critical role of heat in 3D printing, offering guidance for better heat management during the printing process.
Key Factors That Influence Heat Distribution in 3D Printing
When it comes to heat distribution, several factors are at play. First, the type of material you’re printing with matters—materials like PLA, ABS, and PETG each have different temperature requirements. Next, print speed comes into play. If you’re printing too fast, the layers might not have enough time to cool and set evenly. Nozzle temperature and bed temperature are also big factors. If your nozzle is too hot or too cold, it could lead to uneven extrusion, while the bed temperature plays a big role in making sure the first layers stick properly.
Heat Modeling Software and Tools for 3D Printing
Lucky for us, there are a bunch of tools out there that make heat modeling easier. Popular 3D printing slicers like Cura and PrusaSlicer actually include some basic heat modeling features, helping you adjust settings to ensure an even distribution of heat. There are also more advanced heat modeling tools available that provide super detailed simulations, giving you the ability to predict how heat will behave in more complex prints. These tools are like having a 3D printing expert right by your side—minus the coffee breaks.
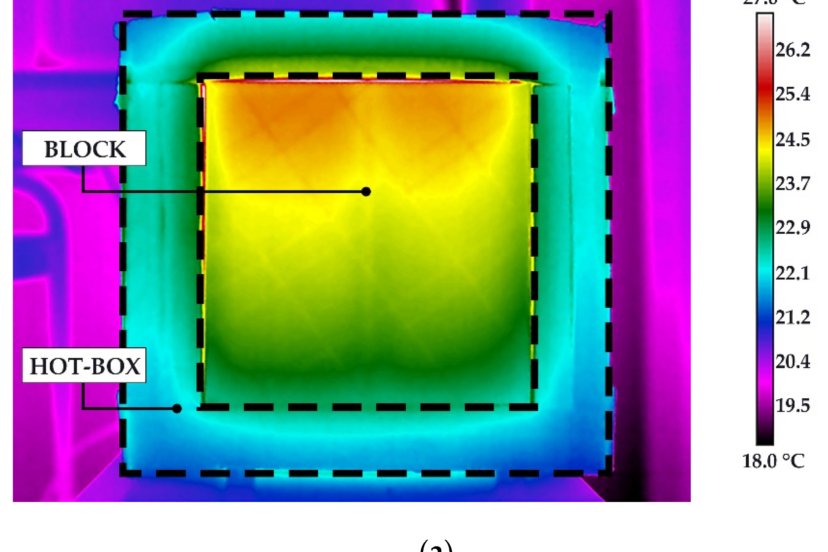
Heat Management in Different 3D Printing Technologies
Not all 3D printing technologies are the same, so heat management can differ depending on which one you’re using. For instance, FDM (Fused Deposition Modeling) printers rely heavily on heat to extrude filament, so controlling temperature is crucial. On the flip side, SLA (Stereolithography) printers use light to cure resin, meaning heat isn’t as big of a concern in the same way. But no matter what technology you’re using, the basic goal is the same: keep the heat evenly distributed for a smooth, high-quality print.
The Impact of Cooling Fans on Heat Distribution
Cooling fans are often the unsung heroes in the 3D printing process. But, if used incorrectly, they can also mess up your print. Too much cooling can cause layers to solidify too quickly, leading to warping or cracking. Not enough cooling, and the print might retain too much heat, making it prone to defects. The key is finding that sweet spot. Heat modeling can help adjust the fan settings so that cooling is applied at just the right rate.
Heat Modeling in Large-Scale 3D Prints
Larger prints are trickier when it comes to heat distribution. They have more surface area, which means they’re more likely to cool unevenly. Without proper heat modeling, larger prints could warp or even break apart. For big prints, it’s essential to use heat modeling to adjust print settings, ensuring the print cools consistently. It’s like trying to cook a giant roast evenly—you need to adjust the heat distribution to avoid any cold spots.
How to Use 3D Print Heat Modeling in Your Workflow
Using 3D print heat modeling in your workflow doesn’t need to be complicated. Start by choosing a slicer with heat modeling features, then tweak your print settings based on the software’s recommendations. You can adjust the nozzle temperature, bed temperature, print speed, and cooling fan settings to make sure the heat is distributed evenly. If you’re working with more complex prints or larger objects, you might want to try more advanced heat modeling software. Test out these changes with smaller prints to see how they affect the quality before going big.
Essential Products for Optimal 3D Print Heat Modeling
To get the most out of 3D print heat modeling, having the right equipment and tools can make a world of difference. Here’s a list of some recommended products that can help ensure your prints come out with perfect heat distribution and top-notch quality:
- Prusa i3 MK3S+ 3D Printer
A reliable FDM printer that offers excellent heat management features like a heated bed and automatic mesh bed leveling for consistent heat distribution. - Cura Slicer Software
This slicer includes advanced heat modeling features to adjust your printer’s temperature settings based on the print’s complexity, ensuring smoother prints. - MatterControl
A powerful 3D printing software that includes features for optimizing heat distribution and monitoring temperature changes throughout the printing process. - Anycubic Photon Mono M7 3D Printer
This resin printer offers a steady temperature control system that helps prevent uneven curing and provides reliable results for high-quality prints. - V6 Volcano Hotend
A hotend that allows for better temperature management, making it easier to control the extrusion rate and nozzle temperature, leading to more consistent heat application during the print.
These tools and products can significantly improve your ability to manage and model heat distribution in your prints, leading to better quality and fewer print failures.
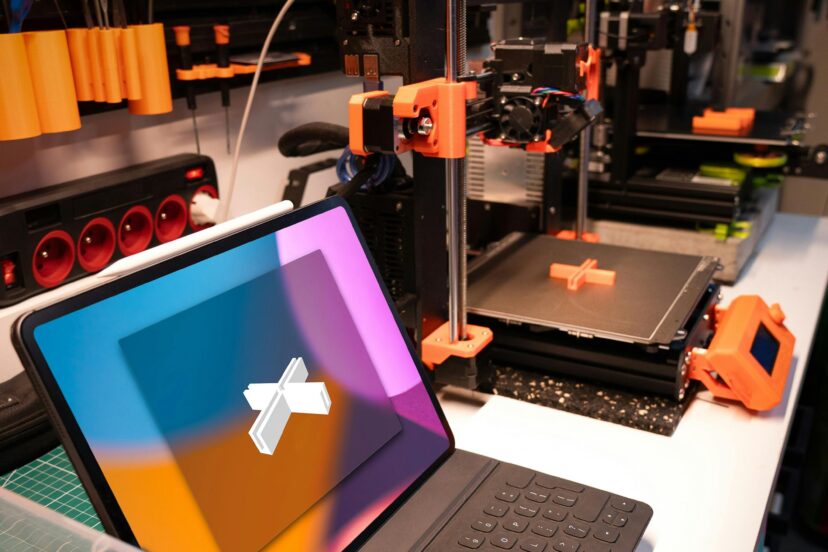
Benefits of Using 3D Print Heat Modeling
There are plenty of reasons to incorporate heat modeling into your printing routine. For one, it can greatly improve print quality. By making sure the heat is evenly distributed, you’ll reduce common issues like warping, cracking, and poor adhesion. It also saves you time and material. Fewer failed prints means you’re not wasting filament or hours of your time. Plus, if you need your print to be precise, heat modeling can help you achieve tighter tolerances.
Common Challenges with Heat Modeling
While heat modeling is a game-changer, it’s not always a perfect solution. It requires a bit of know-how, and it might take some time to fully understand how to use it to its full potential. Different printers and materials may need different settings, and experimenting with those settings can be a bit trial and error. But don’t let that scare you off—once you get the hang of it, it becomes second nature.
Conclusion
To wrap things up, heat distribution is one of the most important factors in achieving high-quality 3D prints. By understanding how heat modeling works, you can prevent issues like warping, cracking, and poor layer adhesion, giving you smoother, more precise prints. Whether you’re just starting out or you’re a seasoned pro, using heat modeling in your workflow can make a huge difference in the final product. So, give it a try next time you print, and watch your results improve!
FAQs
- What is 3D print heat modeling? It’s the process of simulating and managing heat flow during 3D printing to ensure even temperature distribution and improve print quality.
- How does uneven heat affect 3D prints? Uneven heat can cause warping, cracks, poor layer adhesion, and inconsistent surface quality, ruining your print.
- What factors influence heat distribution in 3D printing? Material type, print speed, nozzle temperature, and bed temperature all impact how heat is distributed during the print.
- Can heat modeling prevent warping? Yes! By ensuring even heat distribution, heat modeling helps prevent warping and other issues related to temperature inconsistencies.
- Is heat modeling software necessary for 3D printing? While not absolutely necessary, heat modeling software can significantly improve print quality, especially for complex or large prints.